In 2006, GAC Research and Development (R&D) Center emerged as the technology management powerhouse and the central hub for research and development within the GAC Group. At its core, this centre shoulders the weighty responsibility of steering product development, crafting and executing technology blueprints, and orchestrating the management strategy for the entire GAC Group.
Global reach and cutting-edge facilities
The GAC R&D Center, bolstered by research and development arms in the United States and GAC Advanced Design Shanghai, has stitched together a GAC global R&D network. This network, headquartered in Guangzhou, serves as a melting pot for top-tier suppliers and R&D institutions from across the world.
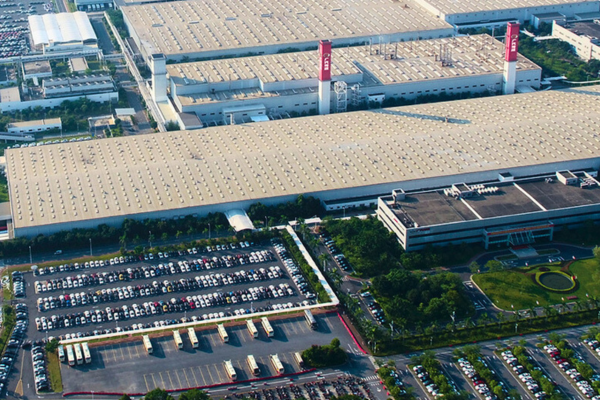
The center boasts world-class R&D facilities, housing an array of 15 specialised labs encompassing vehicle, powertrain, new energy, and Intelligent Connected Vehicle (ICV) research. A trial production factory is also on-site, churning out 800 sample vehicles annually.
Investment and a global brain trust
An investment of over 30 billion yuan has been channelled into independent research and development endeavours. The GAC R&D Center’s workforce of over 4,300 employees; 92 percent of which hold at least a bachelor’s degree, with 110 employees boasting a PhD.
Under the guidance of a top-tier team of experts, a global R&D workforce has been curated, including luminaries from Germany, Italy, the United States, Japan, South Korea, and beyond.
Leadership at the helm
Leading the charge at the GAC R&D Center are luminaries like Wu Jian, President of GAC R&D Center; Zhang Fan, Vice President of GAC R&D Center, and Head of Design Center; Marco Gilardi, CTO of GAC R&D Center and Expert of Chassis Tuning; Pontus Fontaeus, Technical Director of GAC R&D Center and Head of GAC Advanced Design Center Los Angeles; and TABATA Toshiyuki, Technical Director of GAC R&D Center and Expert of NVH Tuning.
A global nexus of innovation
The GAC R&D Center has established collaborative bridges with esteemed universities and research institutions, both domestic and international. Partnerships with the likes of Tsinghua University, Jilin University, South China University of Technology, and others have birthed numerous ongoing projects, magnetizing talents and innovation from around the globe.
The art of crafting a GAC Motor
Ever wondered about the meticulous craft behind a high-quality GAC Motor? The production line unfolds a saga of lean and intelligent manufacturing, ensuring the pinnacle of quality.
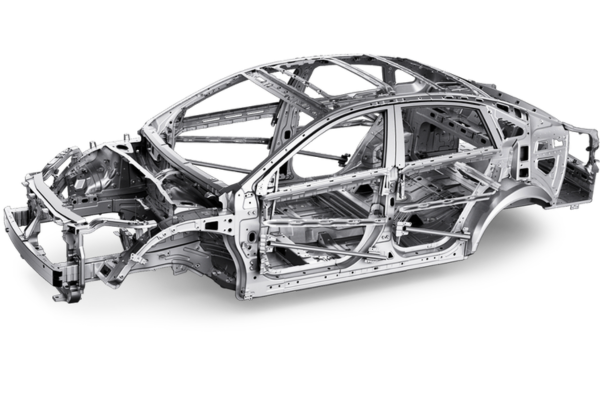
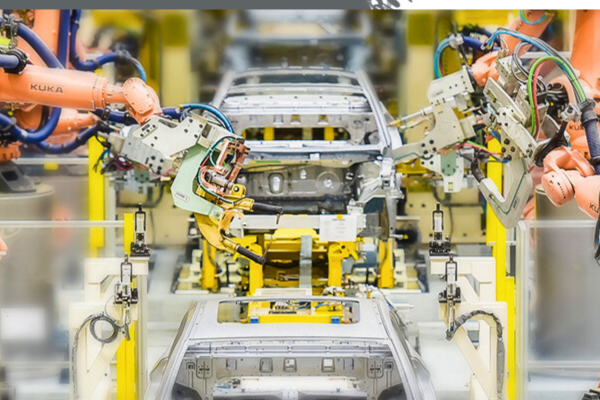
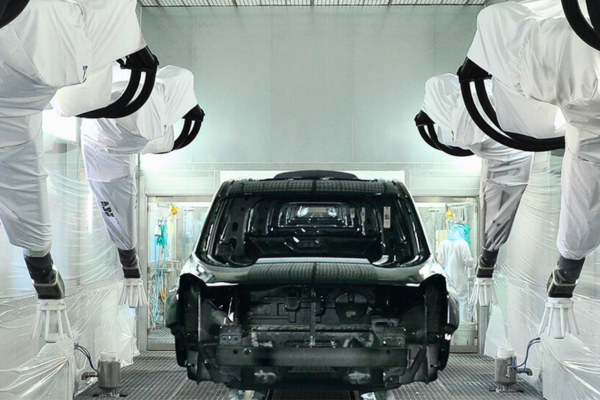
The GAC Motor factory stands as a testament to automation, digitization, and intelligent management, orchestrated by over 550 smart robots and more than 1000 sets of automatic systems. This manufacturing ecosystem leads to ultra-precision and high efficiency throughout the car manufacturing and assembly process.
The precision production journey
Powertrain Workshop:
This houses world-class 6-bar servo presses and 8-bar mechanical presses, paired with 7-axle AGVs, ensuring high-quality and high-precision pressing of complex workpieces.
Stamping:
GAC Motor’s industry-leading stamping technology features advanced CNC hydraulic die cushion, 7-axis robots, and 3D simulation technology. It achieves 100 percent automation in uncoiling blanking line, laser blank welding, and press forming.
Welding workshop:
With over 400 robots, the welding process is 100% automatic, leveraging smart monitoring systems and RFID technology for real-time welding condition adjustments.
Painting Workshop:
This fully-automatic painting line employs 3D image-based recognition systems and robotic precision to ensure impeccable painting and assembly, all while using environmentally friendly water-based paint.
Powertrain workshop:
GAC MOTOR’s powertrain plant organizes production with the utmost precision, ensuring every motor meets premium quality standards.
Final Assembly:
ABB robots, with image-based recognition and positioning systems, achieve unparalleled precision during final assembly.
Vehicle testing line:
Rigorous testing procedures, including static mandatory testing and side-slip measurements, guarantee the function and safety of every vehicle before delivery.
Tire installation:
Intelligent robots ensure precise tire installation, with fault-proof tightening technology for bolt installation.
Exterior assembly:
Robots complete the assembly of front seats, automotive interiors, doors, and more, all with 3D visual tracking for maximum precision.
Quality control:
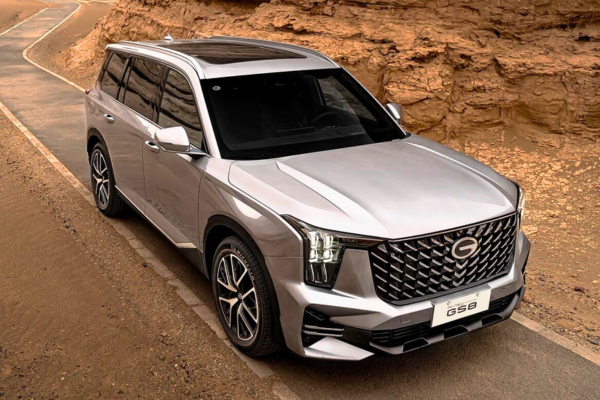
Every GAC MOTOR vehicle undergoes 42 quality control procedures and over 3000 inspections or tests before being deemed ready for sale.
Mastering production with data:
GAC MOTOR’s data architecture platform excels in real-time big data statistical analysis, ensuring every detail is meticulously controlled, from body stitching to screw torque.
At every step, GAC MOTOR employees prioritize quality, forging a comprehensive quality control system that encompasses design, parts, manufacturing, and services.
Each meticulously crafted vehicle undergoes rigorous manufacturing, testing, and inspections, offering an unwavering commitment to safety for every customer.
Read more: GAC Group’s epic journey from zero to $13 billion